To begin with, cars equipped with automatic gearboxes appeared in the United States in the 1940s. As you know, the presence of an automatic gearbox greatly facilitates the vehicle’s operation, reduces the load on the driver, increases safety, etc.
Note that a “classic” automatic gearbox should be understood as a hydromechanical transmission (hydromechanical automatic). Next, we will consider the device of the box – automatic machine, design features, and the advantages and disadvantages of this type of gearbox.
Automatic Gearbox: Advantages and Disadvantages
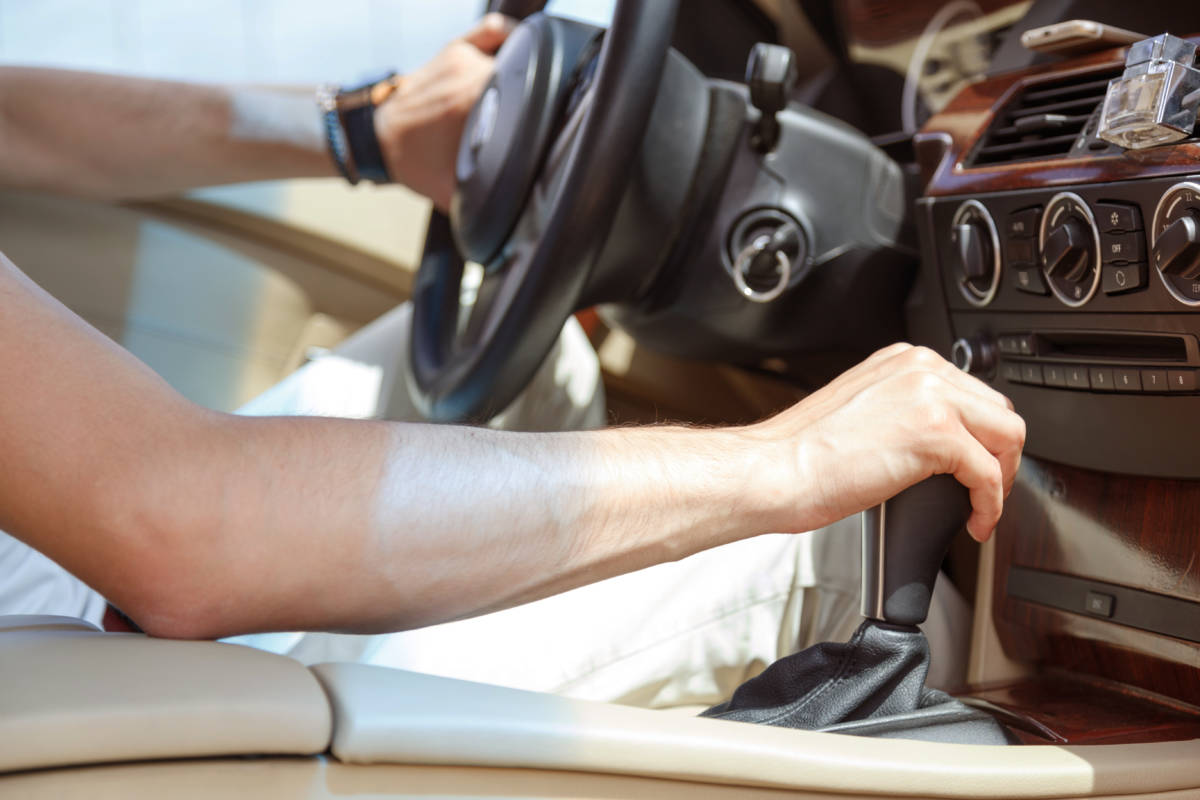
A man driving a car increases the transmission. Details.
Let’s start with the pros. The installation of an automatic gearbox allows the driver not to use the gear lever while driving, and the foot is also not used to squeeze the clutch when going up or down constantly.
In other words, the speed change occurs automatically. That is, the box itself takes into account the load on the internal combustion engine, the vehicle speed, the position of the gas pedal, the driver’s desire to accelerate sharply or move smoothly, etc.
As for the cons, they are also available. First, structurally, the automatic gearbox is a complex and expensive unit characterized by reduced maintainability and resource compared to mechanical (manual) gearboxes. A car with this type of gearbox consumes more fuel; the automatic transmission gives less torque to the wheels since the efficiency of the automatic transmission is somewhat reduced.
Also, the presence of an automatic gearbox in the car imposes certain restrictions on the driver. For example, the automatic gearbox needs to be warmed up before the trip; it is advisable to avoid constant abrupt starts and excessive braking.
A car with an automatic transmission is not allowed to slip, towing a car with an automatic gearbox at high speed for long distances is not allowed without hanging the driving wheels, etc. We also add that such a box is more difficult and more expensive to maintain.
Automatic gearbox: device
So, even taking into account certain disadvantages, an automatic hydromechanical transmission, for several reasons, has long remained the most common solution for changing torque among other types of automatic gearboxes.
First of all, even considering that the resource and performance of such gearboxes are lower than that of the “mechanics”, the hydromechanical gearbox is quite reliable and durable. Now let’s look at the automatic gearbox device.
An automatic gearbox consists of the following basic elements:
- Torque converter. The device performs the function of a clutch by analogy with a manual gearbox. However, the driver does not need to be involved in switching to a particular gear;
- Planetary gear, which is similar to a block of gears in manual “mechanics” and allows you to change the gear ratio when changing gears;
- Brake band and clutches (front, rear clutch) allow smooth and timely gear shifting;
- Automatic gearbox control. This unit includes an oil sump (box pan), a gear pump, and a valve box;
The automatic gearbox is controlled using a selector. As a rule, automatic transmissions have the following main modes:
- P mode – parking;
- R mode – reverse movement;
- Mode N – neutral transmission;
- Mode D – driving forward with automatic gear shifting;
There may be other modes as well. For example, the L2 mode means that only the first and second gears will be engaged when driving forward, the L1 mode indicates that only the first gear is engaged, the S model should be understood as sports, there may be various “winter” modes, etc.
Additionally, an imitation of manual control of the automatic transmission can be implemented. That is, the driver can increase or decrease the gears on his own (manually). We also add that the automatic gearbox often has a kick-down mode (kick-down), allowing the car to accelerate sharply when necessary.
The “kick-down” mode is triggered when the driver sharply presses the gas, after which the box quickly shifts to lower gears, thereby allowing the engine to spin up to high revs.
As you can see, the automatic gearbox actually consists of a torque converter, a manual gearbox, and a control system, which together form a hydromechanical gearbox. Let’s take a look at its structure.
The principle of operation and design of the torque converter
A torque converter is necessary to transmit and change torque from the engine to the gearbox. The torque converter also reduces vibration. The device of the torque converter assumes the presence of a pump, turbine and reactor wheel.
The torque converter also has a lock-up clutch and a freewheel clutch. The torque converter (gas turbine engine, often called “doughnut” in everyday life) is part of the automatic transmission. However, it has a separate housing made of durable material, filled with a working fluid.
A lock-up clutch is required to lock the torque converter in some operating modes. The overrunning clutch or freewheel ensures that the rigidly fixed reactor wheel can rotate in the opposite direction.
Now let’s take a look at how the torque converter works. Its work is based on a closed cycle and consists of gearbox fluid supplied from the impeller to the turbine wheel. Then the liquid flow enters the reactor wheel.
The reactor blades are designed to increase the flow rate of the ATP liquid. The accelerated flow is then redirected to the impeller, causing it to rotate at a higher speed. The result is an increase in torque. You should add that the maximum torque is achieved when the torque converter rotates at the lowest speed.
When the engine crankshaft spins, the angular velocities of the pump and turbine wheels are equalized, while the flow of the gearbox fluid changes direction. Then the freewheel clutch is triggered, after which the reactor wheel begins to rotate. In this case, the torque converter goes into a fluid coupling model; only torque is transmitted.
In modern automatic transmissions, you should note that the operating mode with the slipping of the torque converter lock-up clutch is implemented. This mode excludes complete blocking of the torque converter.
You can realize this mode of operation if the conditions are appropriate when the load and speed are suitable for its activation. The main task of slipping the clutch is the more intensive acceleration of the car, reduced fuel consumption, softer and smoother gear shifting.
What the automatic gearbox consists of how the mechanical part of the box is arranged and works
The automatic transmission itself (automatic transmission), like the mechanical one, changes the torque stepwise when the car moves forward and also allows it to move backwards when the reverse gear is engaged.
At the same time, a planetary gearbox is usually used in automatic transmissions. This solution is compact and allows for efficient work. For example, manual transmissions often have two planetary gears that are connected in series and work together.
Combining gearboxes makes it possible to obtain the required number of stages (speeds) in the box. Simple automatic transmissions have four steps (four-speed automatic), while modern solutions can have six, seven, eight, or even nine steps.
The planetary gearbox includes several sequential planetary gears. Such gearboxes form a planetary gear set. Each of the planetary gears includes:
- sun gear;
- satellites;
- ring gear;
- drove;
The ability to change the torque and transmit rotation becomes available when the elements of the planetary gear are blocked. You can block one or two elements (sun or ring gear, carrier).
If the ring gear is blocked, then an increase in the gear ratio occurs. If the sun gear is stationary, then it will reduce the gear ratio. A blocked carrier means that there is a change in the direction of rotation.
The closing of clutches and brakes is due to hydraulic cylinders. The control of such hydraulic cylinders is realized from a special module (distribution module).
Even in the general design of an automatic gearbox, an overrunning clutch may be present; the task is to hold the carrier, which prevents it from rotating in the opposite direction. It turns out that the gears in the automatic transmission are switched thanks to the clutches and brakes.
Automatic transmission control and the principle of operation of an automatic transmission
As for the automatic transmission principles of operation, the box works according to a given algorithm for turning the clutches and brakes on and off. The control system for switching on and off modern gearboxes is electronic; it has a selector (lever), sensors, and an ECU.
The automatic transmission control unit is integrated into the ECM and is closely related to the engine control unit. By analogy with the engine ECU, the automatic transmission control unit interacts with various sensors transmitting signals about the gearbox speed, transmission fluid temperature, gas pedal position, selector setting modes, etc.
At the same time, there is no clear set algorithm; that is, the transition point to different gears is “floating” and is determined by the ECU box itself. This feature allows the system to work more flexibly.
The valve body (aka hydraulic unit, hydraulic plate, distribution module) actually controls the ATF transmission fluid, responsible for the actuation of the clutches and brakes in the automatic transmission. This module has solenoid valves (solenoids) and special valves, which are interconnected by narrow channels.
Solenoids are needed to change gears, as they regulate the pressure of the working fluid in the box. The operation of these valves is monitored and regulated by the automatic transmission control unit. The valves are responsible for selecting operating modes and are activated using a lever (selector).
The box tends to heat up during operation, so the automatic gearbox often has its own cooling system. At the same time, depending on the design, there may be a separate oil cooler for the automatic transmission or a cooler or heat exchanger, which is included in the general cooling system of the power unit.
What is the bottom line?
Given the above information, it becomes clear that an automatic transmission is complex mechanical, hydraulic, and electronic devices. In this case, the control is carried out both by hydraulics and by an electronic unit.
You should also note that the layout of automatic transmissions may differ between front-wheel drive and rear-wheel drive vehicles, although most of the components are the same.
As for the torque converter, this device can be considered a separate element of the automatic transmission since the gas turbine engine is placed between the engine and the gearbox, performing clutch functions by analogy with the manual transmission.
Also, the oil pump inside the automatic gearbox is driven from the torque converter. The specified pump creates the working pressure of the transmission fluid, which, in turn, allows the gearbox to be controlled.
It turns out that while the internal combustion engine is not working, there will be no pressure on the working transmission fluid in the box. This means that without pressure, it will not be possible to control the automatic transmission, and regardless of which position the selector for selecting the operating mode will be in. Moreover, an attempt to start a car with an automatic machine “from the pusher” can lead to serious damage to the gearbox.
0000000000000000